Tools and Techniques for Inventory Management
For small and medium-sized businesses to compete with global corporations, they need to practice excellent inventory management.
Mismanaging inventory can increase carrying costs, decrease efficiency, and affect customer support. For average businesses, accurate inventory data collection and organization are crucial to remaining competitive.
Small businesses need to incorporate different techniques and tools to improve their order management, increase profitability, and streamline supply chain management. Here are the top inventory management tools to optimize distribution and order fulfillment across multiple warehouses.
Mismanaging inventory can increase carrying costs, decrease efficiency, and affect customer support. For average businesses, accurate inventory data collection and organization are crucial to remaining competitive.
Small businesses need to incorporate different techniques and tools to improve their order management, increase profitability, and streamline supply chain management. Here are the top inventory management tools to optimize distribution and order fulfillment across multiple warehouses.
Inventory Management Best Practices
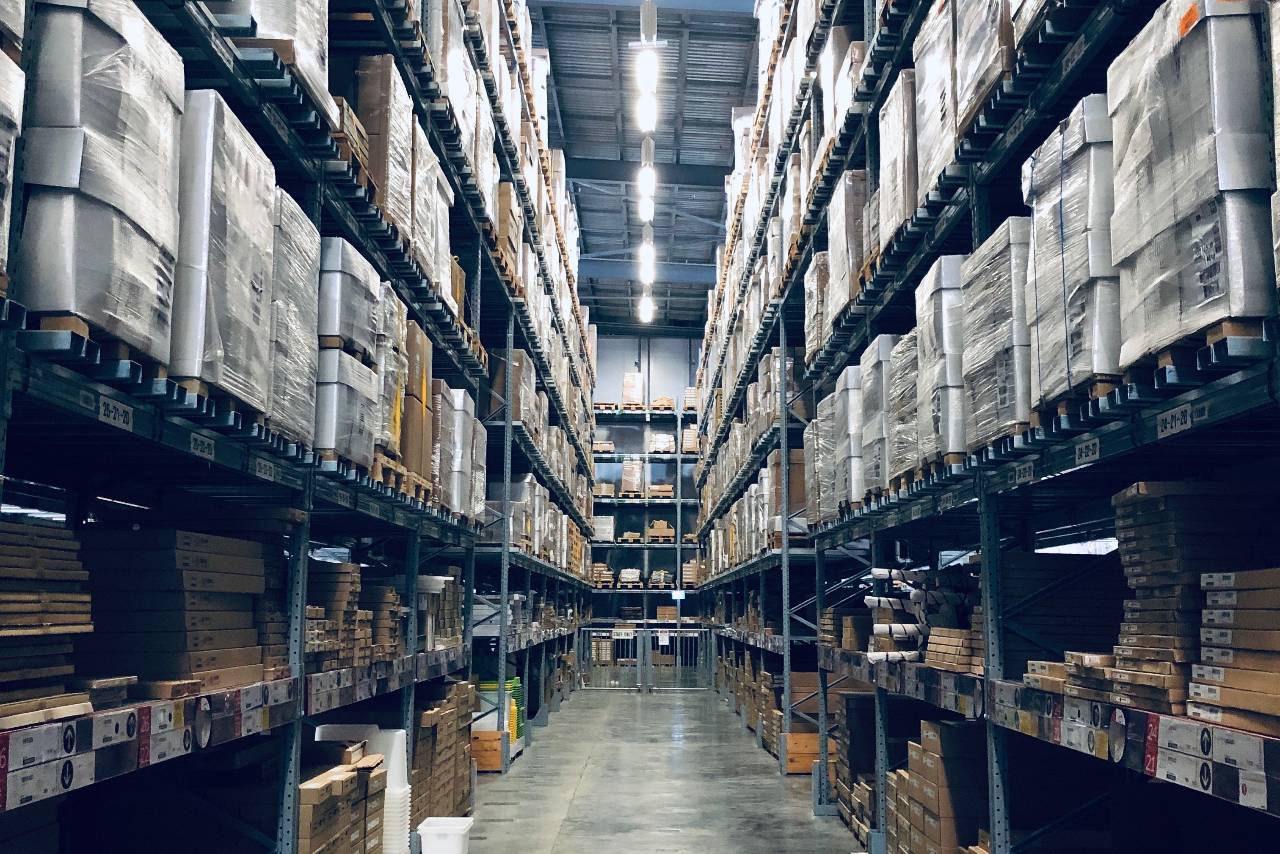
Here are the best inventory management practices to streamline work across multiple channels-
1. Reduce Inventory Levels
Many companies have 20-40% of their working capital (operating liquidity) in retail inventory. Those at the higher end of that percentage should consider reducing real-time inventory to decrease carrying costs and improve their profit margin.
Try using these three methods-
The pick and pack process involves a set of techniques and tools utilized to fulfill purchase orders proficiently and manage stock levels. The pick and pack process includes-
Check each order or use a barcode system to ensure each order is accurately counted. Finally, implement a warehouse management system where items are picked in the order an operator finds them.
3. Pick Quality Inventory KPIs
An inventory KPI measures the performance level of the company's supply chain processes. This will help to eliminate guesswork so workers know exactly which goals to meet every day or week.
Businesses can use metric tracking to collect relevant data that shows which areas are inefficient and need improvement. To pick relevant KPIs, focus on-
Safety stock is a minimal amount of business inventory on-hand that is used to protect against fluctuations in customer demand and lead times. A lack of safety stock may cause a loss in revenue, customers, and a share of the market.
By ensuring operators always have safety stock, a small business will protect itself against unforeseen events, inaccurate forecasts, and extra-long lead times.
1. Reduce Inventory Levels
Many companies have 20-40% of their working capital (operating liquidity) in retail inventory. Those at the higher end of that percentage should consider reducing real-time inventory to decrease carrying costs and improve their profit margin.
Try using these three methods-
- Lower Lead Times- Track current lead times or the time between the completion and fulfillment of the order in the warehouse. Share sales data with vendors and see if minimum order quantities can be reduced to lessen the amount of stock on-hand per month.
- Discard Obsolete Inventory- Offer a discounted price on discontinued inventory or try dating it to write the inventory off on taxes.
- Improve Predictive Analysis- Use a cloud-based software solution to improve forecasting, collect real-time data, and conduct accurate reporting. This will help to gain valuable insights that allow inventory managers to make better business decisions.
The pick and pack process involves a set of techniques and tools utilized to fulfill purchase orders proficiently and manage stock levels. The pick and pack process includes-
- Discrete Order Picking- A worker goes through and completes one order at a time.
- Batch Picking- Operators fill all orders in a batch at one time and then move on to another batch until every order is fulfilled.
- Wave Picking- The process of combining many orders in a batch to reduce the required number of pick-up trips.
- Zone Picking- Pickers are assigned and sort through a set of SKUs in a particular zone.
Check each order or use a barcode system to ensure each order is accurately counted. Finally, implement a warehouse management system where items are picked in the order an operator finds them.
3. Pick Quality Inventory KPIs
An inventory KPI measures the performance level of the company's supply chain processes. This will help to eliminate guesswork so workers know exactly which goals to meet every day or week.
Businesses can use metric tracking to collect relevant data that shows which areas are inefficient and need improvement. To pick relevant KPIs, focus on-
- Carrying Costs- The total expenses related to the storage of unsold products.
- Inventory Write- Off A formal recognition to declare a company's inventory no longer has value.
- Inventory Turnover Rate- A ratio that demonstrates how many times inventory has been replaced during a given time frame.
- Cycle Time- The amount of time spent producing an item before it ships.
- Order Status and Tracking- The SKUs currently in the warehouse and the time spent to ensure a tracking number is placed on each item and sent to its final location.
- Fill Rate- The fraction of client demand that is met through immediate inventory availability.
Safety stock is a minimal amount of business inventory on-hand that is used to protect against fluctuations in customer demand and lead times. A lack of safety stock may cause a loss in revenue, customers, and a share of the market.
By ensuring operators always have safety stock, a small business will protect itself against unforeseen events, inaccurate forecasts, and extra-long lead times.
Top 5 Tools to Manage Inventory
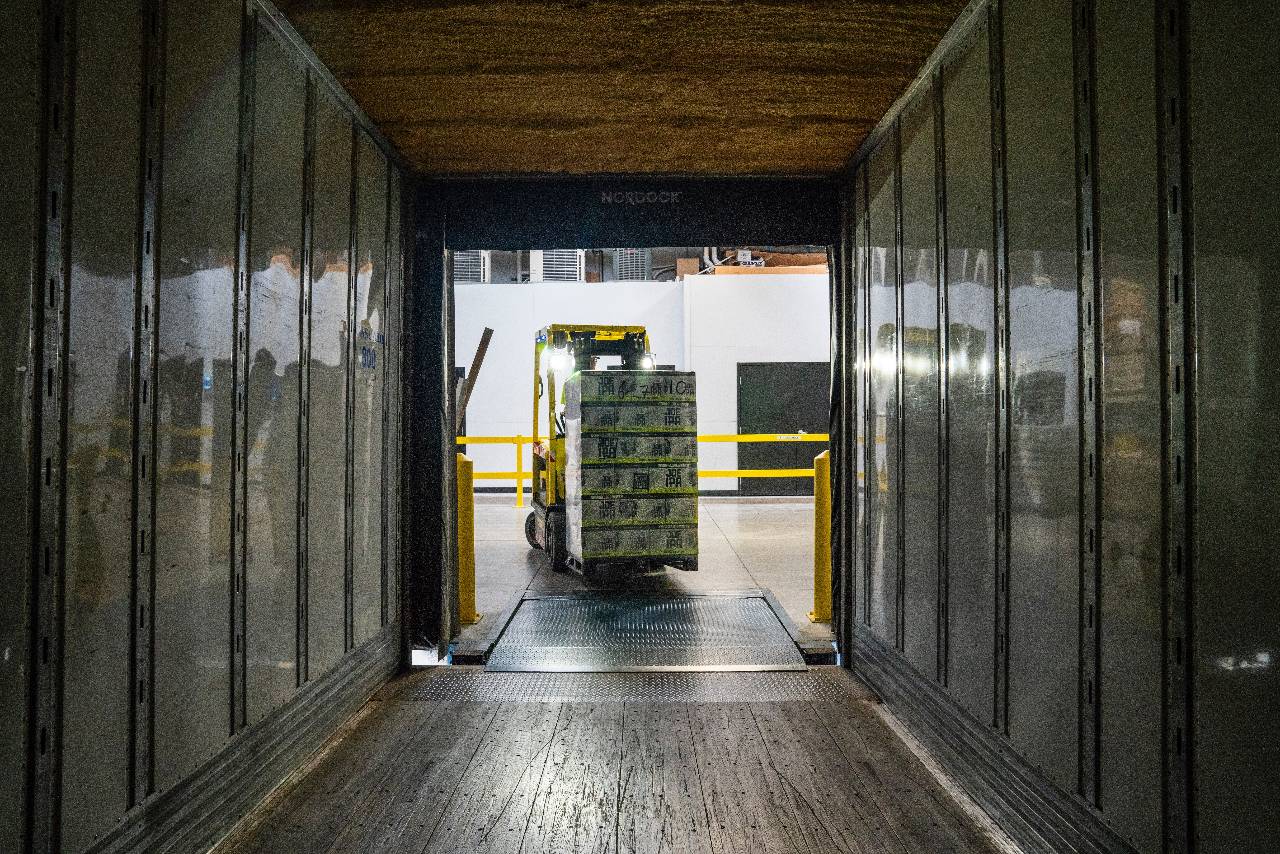
To further improve inventory management techniques, consider utilizing the following inventory management systems and tools-
1. Barcode Data Collection
Manual reporting leaves plenty of opportunity for human error and inaccuracy. Because having reliable data is crucial to inventory optimization, automate data collection by implementing a barcode scanning system.
This will take the burden off the workforce and greatly improve the reliability and accuracy of the company's inventory data.
2. Cycle Counting
Utilizing a cycle counting system to replace the meticulous and labor-intensive physical stock count will improve inventory accuracy and decrease labor costs.
Cycle counting is a process that counts important items more frequently than the less important ones. This method provides a system for verifying and eliminating the place where errors originate in the supply chain.
3. ABC Analysis
Use ABC analysis to arrange items from most to least important. Organizing stock in this fashion will simplify order fulfillment and save space in the warehouse.
In practice, ABC analysis may look like this-
Integrate planning and implementation by incorporating a cloud-based inventory management system into the company's supply chain practices.
An inventory software solution coupled with accounting software will improve inventory data accuracy, increase efficiency, minimize waste, and decrease carrying costs. It is a user-friendly solution that decreases labor expenses by automating many menial and labor-intensive tasks.
A management tool has key features including phone integration capabilities. This allows management to make updates from a mobile app across multiple locations. This will help to increase productivity across all levels of the supply chain.
5. Use Serial Number Traceability
Lot tracking allows the warehouse to track inventory along the distribution chain until an item is shipped. Accurate serial number tracking is valuable to product development, engineering, inventory management, and other areas of the company.
Serial number traceability will increase financial accountability and maximize efficiency throughout all areas of the supply chain. It is an important resource for performance management and quality customer service.
1. Barcode Data Collection
Manual reporting leaves plenty of opportunity for human error and inaccuracy. Because having reliable data is crucial to inventory optimization, automate data collection by implementing a barcode scanning system.
This will take the burden off the workforce and greatly improve the reliability and accuracy of the company's inventory data.
2. Cycle Counting
Utilizing a cycle counting system to replace the meticulous and labor-intensive physical stock count will improve inventory accuracy and decrease labor costs.
Cycle counting is a process that counts important items more frequently than the less important ones. This method provides a system for verifying and eliminating the place where errors originate in the supply chain.
3. ABC Analysis
Use ABC analysis to arrange items from most to least important. Organizing stock in this fashion will simplify order fulfillment and save space in the warehouse.
In practice, ABC analysis may look like this-
- A-Items- These are the highest priority items that sell the best. A-items necessitate regular re-ordering and review of their quality.
- B-Items- B-items are medium quality, average priority products that are reordered on a somewhat consistent basis.
- C-Items- C-items are low-priority goods that don't sell very well and aren't re-ordered very often.
Integrate planning and implementation by incorporating a cloud-based inventory management system into the company's supply chain practices.
An inventory software solution coupled with accounting software will improve inventory data accuracy, increase efficiency, minimize waste, and decrease carrying costs. It is a user-friendly solution that decreases labor expenses by automating many menial and labor-intensive tasks.
A management tool has key features including phone integration capabilities. This allows management to make updates from a mobile app across multiple locations. This will help to increase productivity across all levels of the supply chain.
5. Use Serial Number Traceability
Lot tracking allows the warehouse to track inventory along the distribution chain until an item is shipped. Accurate serial number tracking is valuable to product development, engineering, inventory management, and other areas of the company.
Serial number traceability will increase financial accountability and maximize efficiency throughout all areas of the supply chain. It is an important resource for performance management and quality customer service.
Conclusion
Here are the key takeaways to remember about inventory management-
- Proper inventory management will decrease carrying costs, improve efficiency, and increase customer satisfaction.
- Tips to manage inventory accurately include stock reduction, effective picking and packing, choosing quality KPIs, and carrying safety stock.
- The best tools to manage inventory include barcode data collection, cycle counting, ABC analysis, an inventory management software system, and serial number traceability.