Understanding the Supply Chain Process
The supply chain process encompasses a series of steps that ensure the flow of finished goods or services to customers. By developing a successful and well-defined supply chain, businesses will be able to effectively oversee their operation and guarantee overall customer satisfaction.
Elements of the Supply Chain Process
The supply chain generally begins with manufacturers and producers who create products from raw materials. It is then transported and distributed to other suppliers and vendors who will either further transform the goods or sell the finished product to consumers.
To curate a productive supply chain, businesses must understand its 3 elements. First are the external suppliers, which are organizations that provide goods, parts of a product, or services. For example, a dairy farmer, paper mill, and tech support specialist would classify as external suppliers.
The second element of a supply chain is the company's internal functions and procedures to produce a product. Following the previous example of a dairy farmer, the farm's process of transforming raw milk into various dairy products and packaging them for consumer consumption is an internal function.
Lastly, external distributors are the third component of the supply chain. These are organizations responsible for transporting and delivering finished goods from the producer or manufacturer to retailers. With the effective collaboration of all three aspects, the supply chain is able to smoothly and promptly move goods to fulfill customer demands.
Along with these 3 components, there are 5 strategic steps to a supply chain process-
To curate a productive supply chain, businesses must understand its 3 elements. First are the external suppliers, which are organizations that provide goods, parts of a product, or services. For example, a dairy farmer, paper mill, and tech support specialist would classify as external suppliers.
The second element of a supply chain is the company's internal functions and procedures to produce a product. Following the previous example of a dairy farmer, the farm's process of transforming raw milk into various dairy products and packaging them for consumer consumption is an internal function.
Lastly, external distributors are the third component of the supply chain. These are organizations responsible for transporting and delivering finished goods from the producer or manufacturer to retailers. With the effective collaboration of all three aspects, the supply chain is able to smoothly and promptly move goods to fulfill customer demands.
Along with these 3 components, there are 5 strategic steps to a supply chain process-
1. Planning
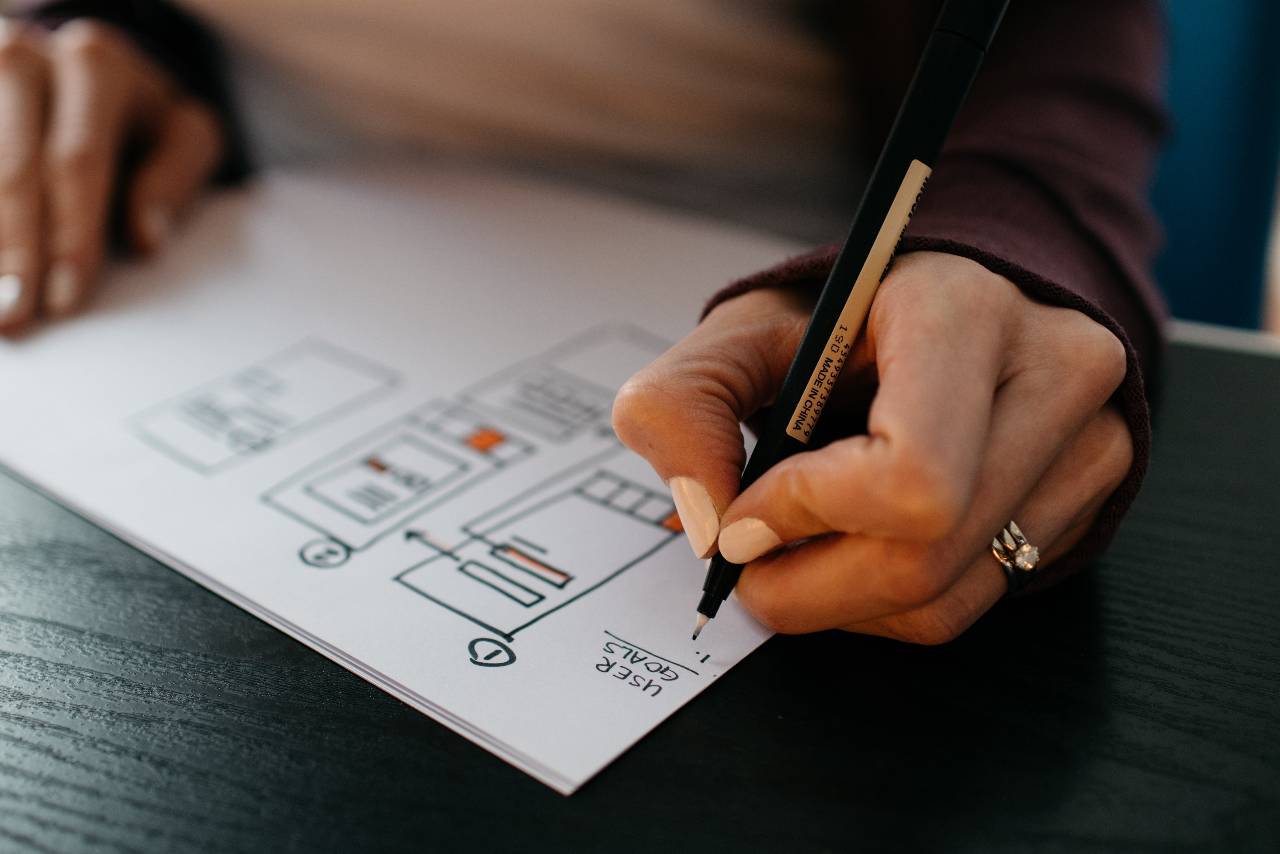
To begin developing a supply chain process, companies need to plan out how they will operate. For example, if a business is selling a children's toy, then the owners need to strategize if they will purchase the toy's components from a supplier, manufacture the component, or buy the entire toy from a production facility.
In the case that the company decides to manufacture the entire product, they must then identify which raw material supplier they should work with. Additionally, management teams need to decide how the goods will be produced. For example, they can be produced and stored in inventory, be made-to-order, or be partially manufactured and finished when a customer places an order.
The supply chain planning stage also requires designing and organizing the company's warehouse, manufacturing plant, and stores to ensure efficient travel time between sites. Executives should also establish key performance indicators (KPIs) and collect data about the market to project and keep track of their productivity.
By comprehensively planning, companies can align their supply chain to their business model, ensure collaboration between all parties within the network, and monitor the effectiveness of their strategies.
In the case that the company decides to manufacture the entire product, they must then identify which raw material supplier they should work with. Additionally, management teams need to decide how the goods will be produced. For example, they can be produced and stored in inventory, be made-to-order, or be partially manufactured and finished when a customer places an order.
The supply chain planning stage also requires designing and organizing the company's warehouse, manufacturing plant, and stores to ensure efficient travel time between sites. Executives should also establish key performance indicators (KPIs) and collect data about the market to project and keep track of their productivity.
By comprehensively planning, companies can align their supply chain to their business model, ensure collaboration between all parties within the network, and monitor the effectiveness of their strategies.
2. Obtaining Goods
Once businesses have planned out who their suppliers will be, they must arrange contracts and set standards for delivery schedules and payments. Companies should ensure thorough communication with all suppliers, as well as track and manage inventory to maintain proper stock levels.
Performance of suppliers, such as lead times, should also be frequently assessed to make sure the requirements of delivery and products are met.
Performance of suppliers, such as lead times, should also be frequently assessed to make sure the requirements of delivery and products are met.
3. Producing
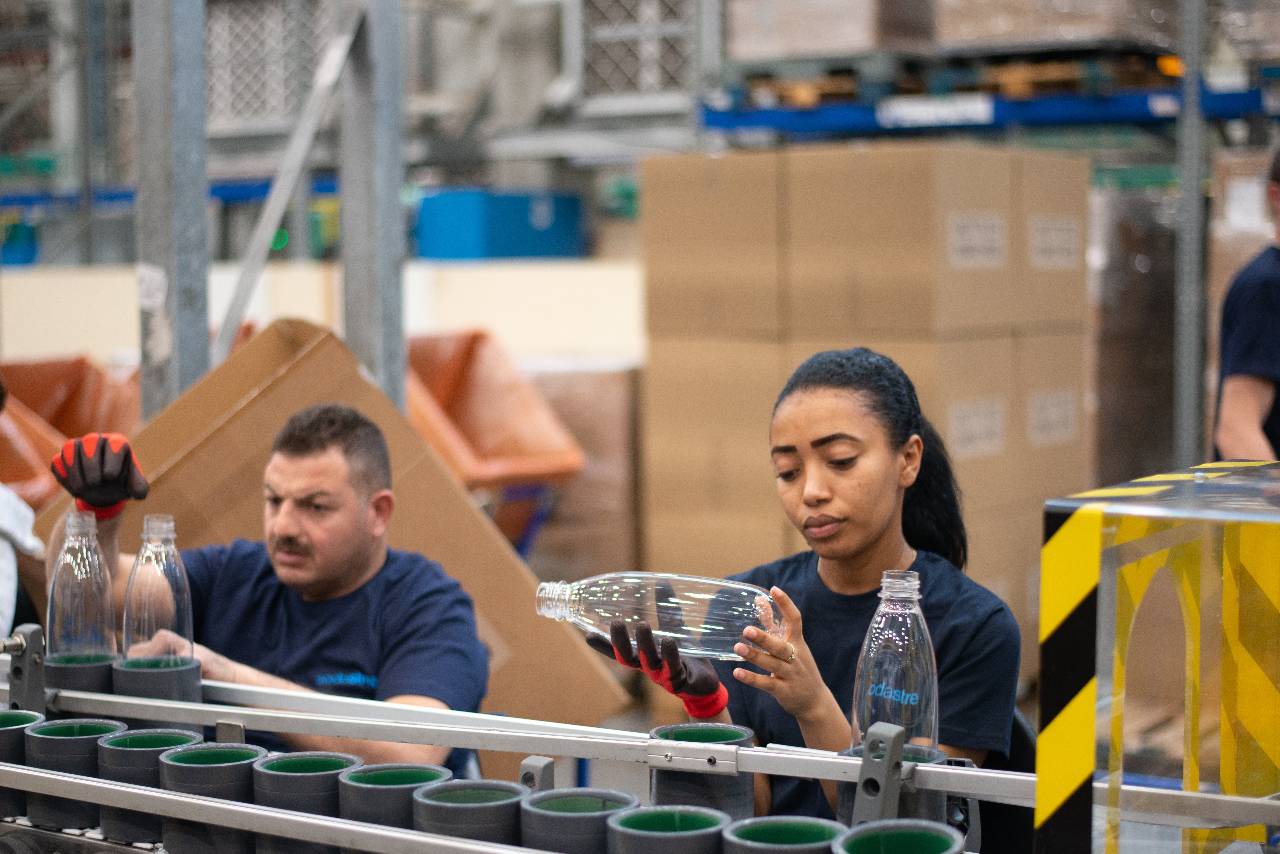
At this stage, businesses are testing goods, manufacturing or assembling the final products, and packaging them for consumers. To make sure that the business is meeting production goals, data regarding employee and sales performance should be monitored. This will enable management to make necessary adjustments to employee schedules or production levels.
Managers should also create compliance standards for facilities to ensure that products and supplies are properly treated, stored, and disposed of.
Managers should also create compliance standards for facilities to ensure that products and supplies are properly treated, stored, and disposed of.
4. Delivering Products
Not only does the delivery stage involve distributing and transporting finished goods to retailers and consumers, but it also encompasses answering inquiries that customers have about a product.
Businesses should also be conducting inventory management to make sure products are organized in the warehouse, stored appropriately, and monitored to prevent obsolescence.
To streamline this process, management should implement a digital inventory management solution. These cloud-based tools enable authorized users to accurately track inventory, as well as send orders and automate invoices.
Businesses should also be conducting inventory management to make sure products are organized in the warehouse, stored appropriately, and monitored to prevent obsolescence.
To streamline this process, management should implement a digital inventory management solution. These cloud-based tools enable authorized users to accurately track inventory, as well as send orders and automate invoices.
5. Processing Customer Returns
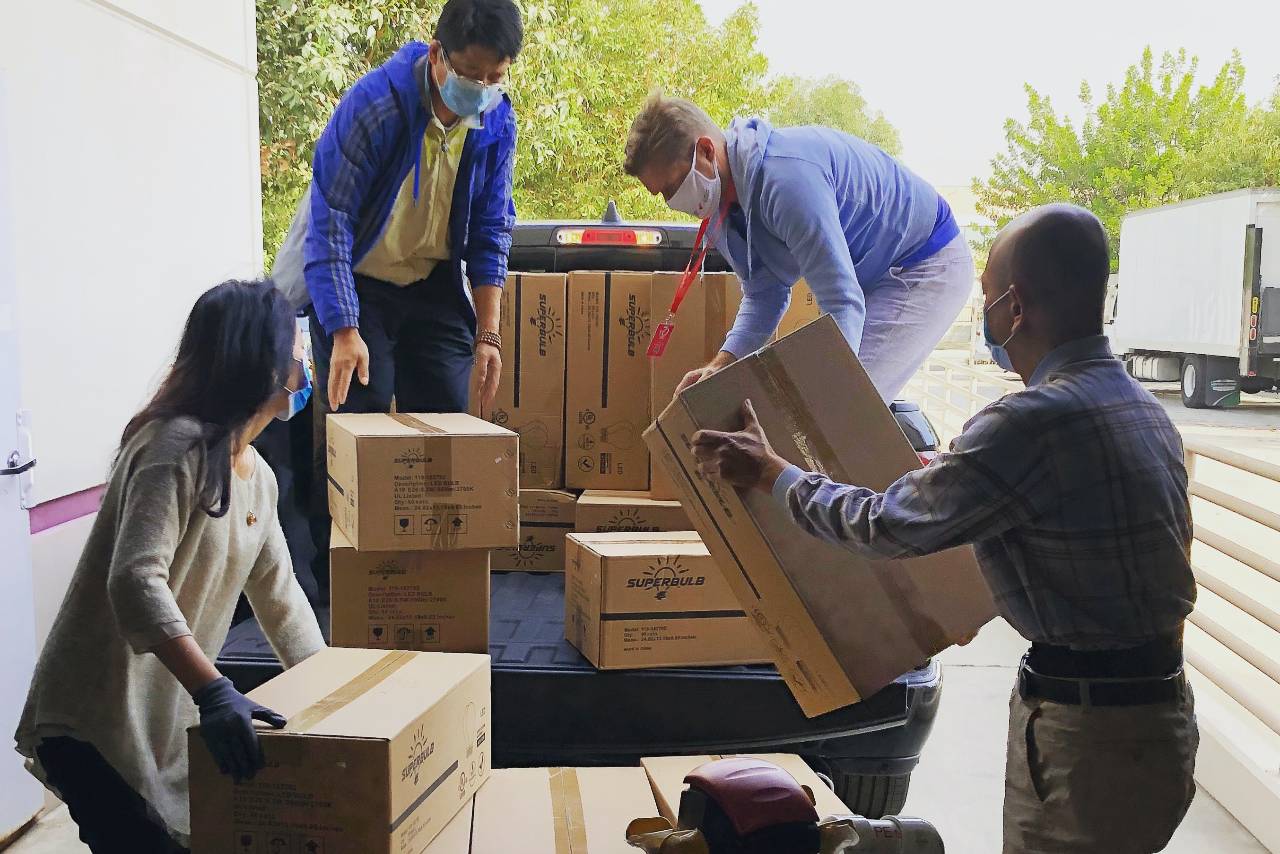
Processing and managing returns are often necessary when dealing with defective products. At this stage, employees must identify the condition of the item and its flaws, authorize customer returns, process refunds, and replace obsolete items with new ones. This will enable positive customer service and can improve customer relationship management.
Products that are at the end of their lifecycle, meaning they no longer have market demand or value, are also monitored at this stage because they contribute to the inventory of unsalable and returned items. It is important to assess product performance and conduct frequent quality control to prevent extra costs to carry and remove unwanted products from the warehouse.
Products that are at the end of their lifecycle, meaning they no longer have market demand or value, are also monitored at this stage because they contribute to the inventory of unsalable and returned items. It is important to assess product performance and conduct frequent quality control to prevent extra costs to carry and remove unwanted products from the warehouse.
Key Takeaways
- An effective supply chain process ensures goods are created and delivered to customers.
- There are 3 elements to a supply chain- external suppliers, internal processes, and external distributors.
- The 5 stages of a supply chain process are planning, obtaining goods, producing, delivering, and returning.
- To streamline supply chain management and monitor inventory, businesses should use inventory administration software.